実際に代表の奥村が携わり成果を出した事例を2つご紹介します。
コンセプト
これからお伝えする2つの事例から言えること
お金をかけなくても工夫で設備能力は上げられる
慣習にとらわれない発想が成功の秘訣
現状を可視化することで
問題が見えてくる
予備知識
「山積み票」をご存じでしょうか?
「山積み票」とは、作業改善を考える
アイテムのひとつ
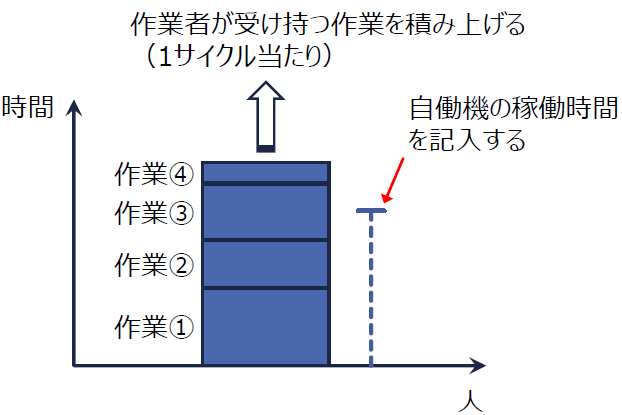
作業者と機械のバランスを
観るアイテム
山積み票の見方
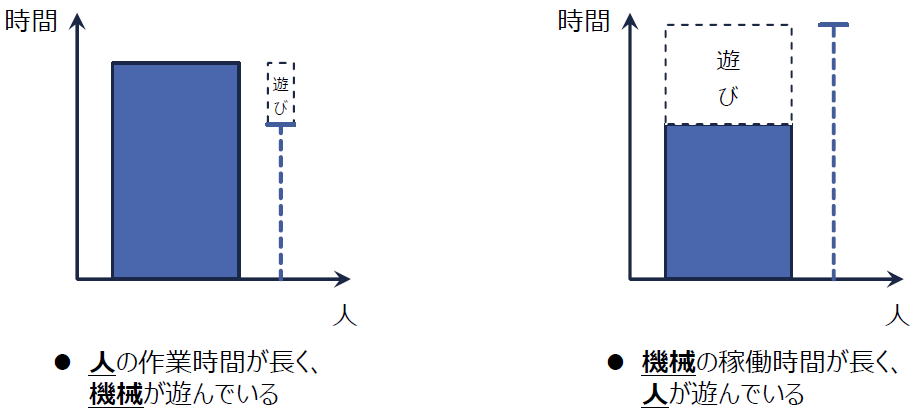
山積み票から改善のターゲットが
見えてくる
では、ここから実際の改善事例をご紹介します。
事例① 作業分配の見直し
改善前の状況
求められた生産量は従来の150%、その約60%が当該設備で処理する製品で、当該設備の能力向上が生産量達成のキーとなっていた。さらに当時、需要が特に多く、利益率の高い製品だったため営業からの突き上げもかなりあり、改善は急を要する状態であった。
私は毎日1日中現場で作業を観察し、あるとき入側、出側作業のアンバランスに気づき、ネックになっていた出側作業をどのようにすればバランスが取れるかを模索。それの時に大いに役立ったのが数カ月前の研修で習得したトヨタ式の改善手法であった。
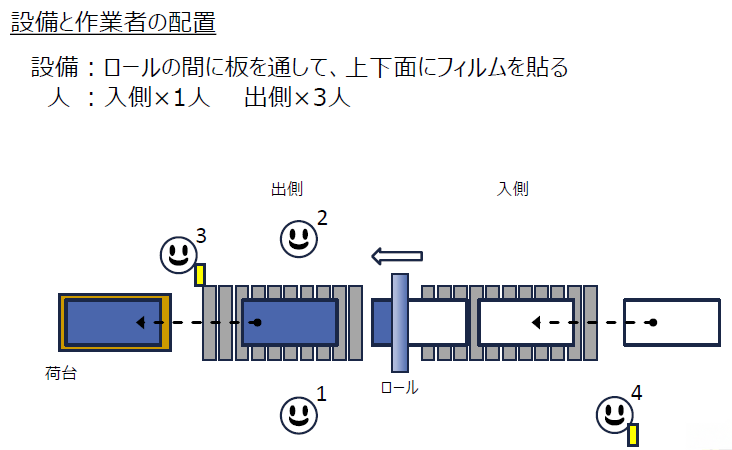
作業者の仕事
1:板を切り離す、余分なフィルムを除去、梱包する
2:板を切り離す、余分なフィルムを除去、梱包する
3:フィルム除去が終わったら板を荷台に運搬する
1,2が梱包中はフィルム除去
4:テーブルが空いたら板を補充する
作業のほとんどが人手によるもの
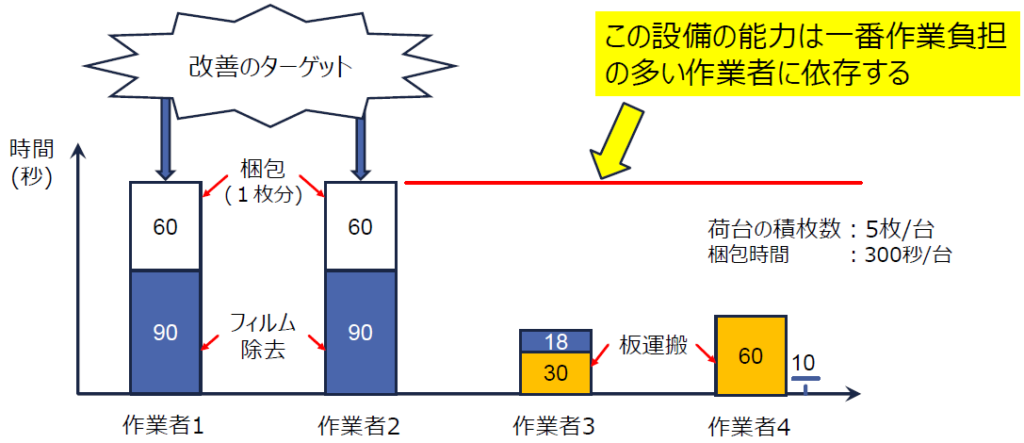
改善後
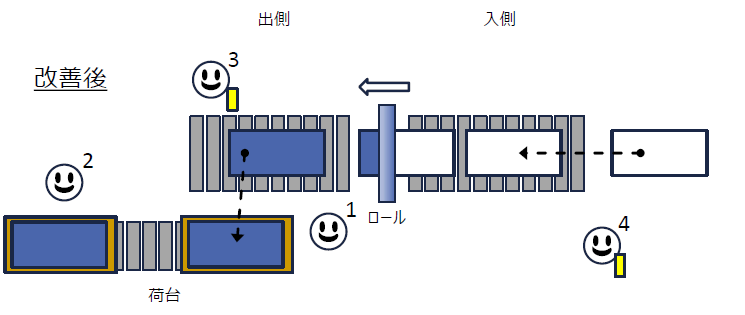
作業者の仕事(赤字:変更点)
1:板を切り離す、余分なフィルムを除去、仮梱包する
2:梱包を完成させる
3:フィルム除去し、板を荷台に運搬し仮梱包する
4:テーブルが空いたら板を補充する
ポイント
- 出側作業のサイクルを短くするため梱包を2回に分けた
- 手待ちの多い作業者3に仕事を分配した
見直しの結果
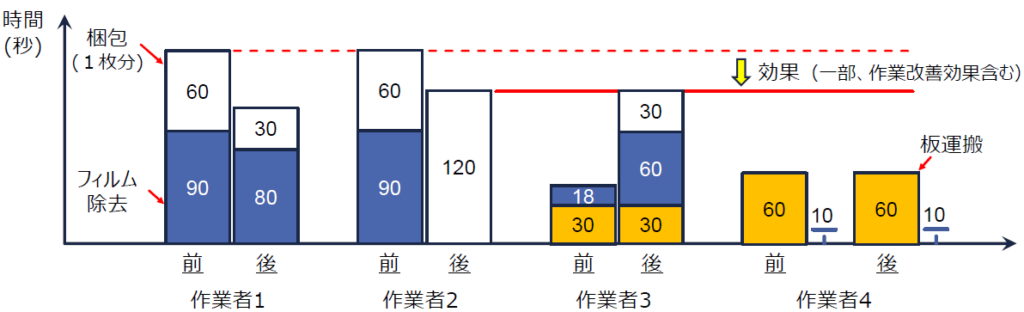
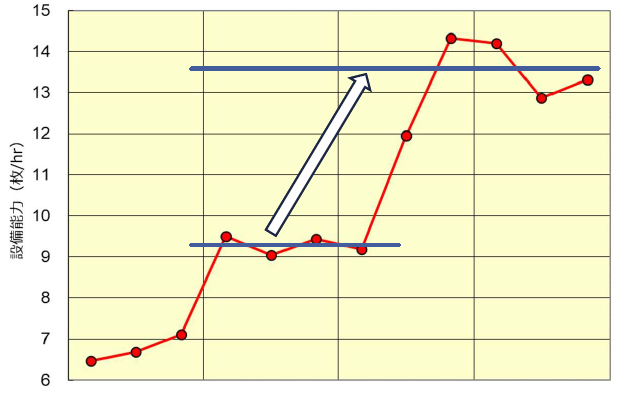
設備能力は従来の1.5倍にアップ
結論:作業者の負担を平準化するだけでも設備の能力を上げることは可能
まとめ
改善により当該設備の生産能力は向上し、目標を達成することができた。
さらに当時は急を要したため、不要パレットの上にコロコンを置いたお粗末なものであったが、現在は移設に伴い設備も整備され、約20年前に作り上げたやり方で行われている。
事例② 平準生産による効率向上
改善前の状況
当該製品は、顧客が造る製品を構成する部品の一つで、顧客の組み立てスケジュールに合わせて納入するため、厳しい納期管理を要求された。さらに焼入れ処理を行うため歪の強制作業や不良による作り直しも発生するため、再制作も発生するため、歩留りを考慮し必要量以上の材料が流れていていたるところに材料が停滞していた。
それを解消したいとの要望で、私が最終的なゴールとして提案したのが、カンバンを導入した後工程引き生産であった。しかし、カンバンを導入するための下地が何もなかったため、まずは平準化生産を行い、材料投入を決める工程担当、現場がなれた後にカンバン生産へ移行することとした。
製品の概要
- 形状の異なる鍛造品6アイテムで1セット
- 1ヶ月単位で6ヶ月前に注文が確定
- 商社が在庫量に応じて発注= 営業は受注量を同数を入票(製作依頼)
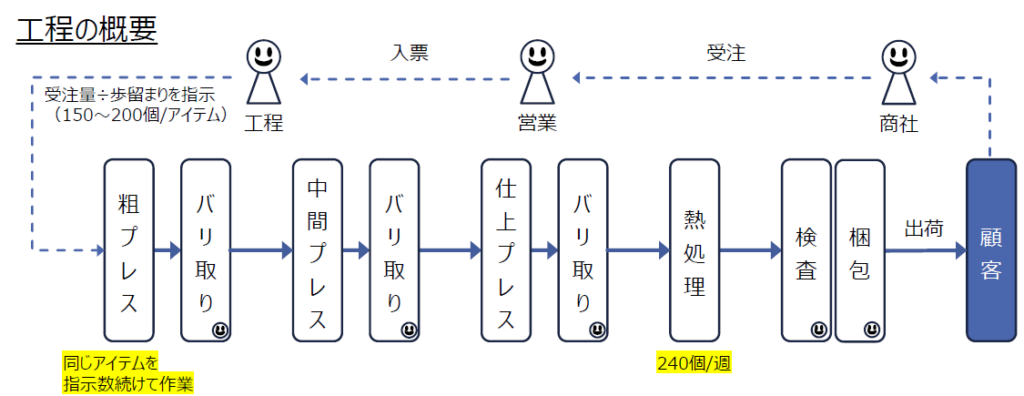
何が起こったのか?
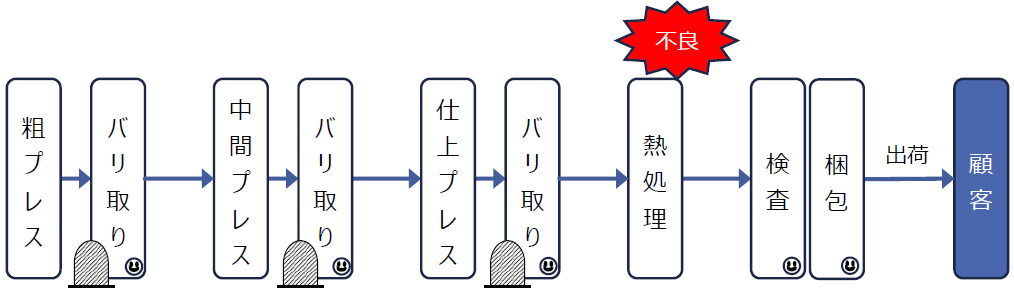
- 能力のないバリ取り前にモノが停滞した
- 熱処理の歩留りが悪く、指示数を下回ると再制作が発生した
リードタイム(改善前)
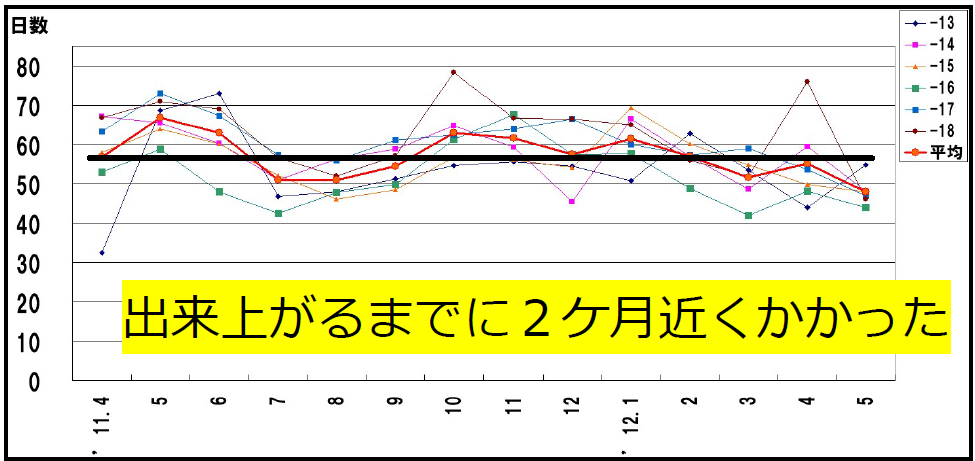
非効率発生の理由
例えば、A、B、C、三種類の製品を加工する機会をイメージしてください。
下のパターンは、A:6回に1個、B:8回に1個、C:10回に1個で造られます。

つまり、造る単位で製造期間が決まるのです。
また、同じものを続けて造ると効率が良くなり安く造れると思いがちですが、大量不良のリスクが高くなることも留意しておく必要があります。
実際の対処法
- 各アイテムの最小単位(20個)を決め、最小単位で作業することとした
- プレス作業の1日のパターンを決めた
- 作業前・後の置き場を明確にした
プレス作業パターン
午前:6アイテム各20個を作業、以後、他製品を作業
午後:仕掛り状況に応じて作業
に変更した結果・・・・
リードタイム(改善後)
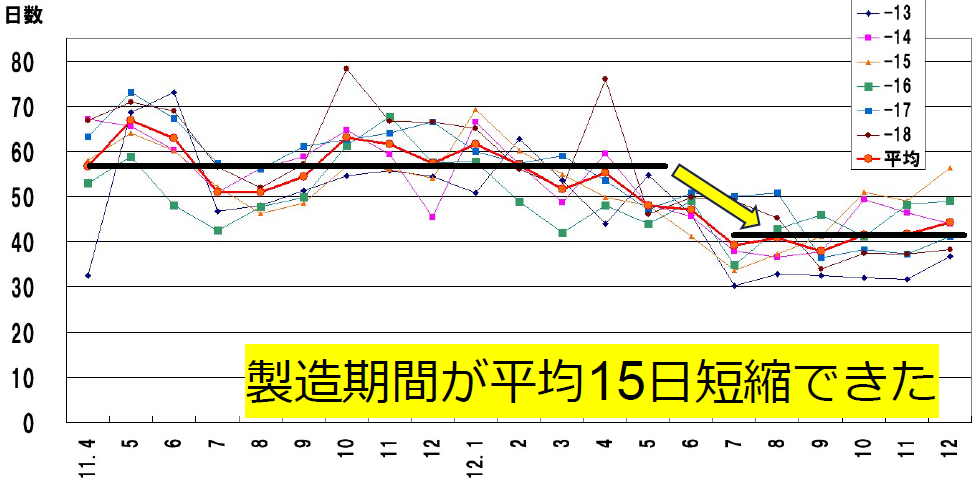
まとめ
設備前の未加工材料の溜まり少なくなり、製造リードタイムも3/4(約45日)に短縮したが、それ以上に効果を感じられたのは工程担当や現場がモノの流し方を変えるだけで生産が楽になると理解してくれたことだった。
それ以来、その会社は改善活動に非常に前向きになり、次のステップへもスムーズに移行でした。
いかがでしたでしょうか?
これ以外にもお金をかけずに生産効率をアップさせた事例をまとめた無料の事例集を差し上げています。